Leading Metal Stamping Solutions for High-Quality and Cost-Effective Production
Leading Metal Stamping Solutions for High-Quality and Cost-Effective Production
Blog Article
Discovering the Globe of Metal Stamping: From Layout to Manufacturing
Within the world of manufacturing, metal marking sticks out as an accurate and effective approach for forming steel sheets into numerous forms with exceptional uniformity. From the first layout phase where detailed patterns take form to the complex production processes, steel stamping is a blend of creativity and design. Exploring this globe introduces a complex interaction of creativity and technological mastery, providing a glimpse right into a realm where technology fulfills craftsmanship.
History of Steel Stamping
Steel stamping, an extensively made use of manufacturing process today, has an abundant background that goes back to old times (Metal Stamping). The origins of metal stamping can be mapped to old human beings such as the Egyptians, that used marking methods to embellish precious jewelry and accessories with detailed designs. Over time, metal marking evolved, with people like the Greeks and Romans utilizing it for producing coins and decorative things

In the 20th century, metal stamping proceeded to develop with the integration of automation and computer mathematical control (CNC) innovation. These improvements additionally enhanced the efficiency and accuracy of metal stamping processes, making it an important component of modern-day production across industries such as automotive, aerospace, and electronics. Today, steel stamping stays a vital production process, integrating tradition with advancement to satisfy the needs of a frequently advancing market.
Layout Considerations and Prototyping
When creating metal marking jobs, thorough interest to develop factors to consider and prototyping is vital for ensuring optimum manufacturing outcomes. Design considerations in metal stamping consist of material selection, component geometry, tooling style, and production expediency. Picking the right product is important as it affects the part's performance, expense, and manufacturability. Component geometry affects the complexity of the marking process and the performance of the end product. Tooling design plays a substantial duty in the success of metal marking jobs, affecting part accuracy, device longevity, great post to read and production efficiency.
Prototyping is click to investigate an important stage in the metal stamping procedure that allows designers to evaluate the layout, verify manufacturability, and make needed adjustments prior to full-scale manufacturing. By carefully considering design facets and using prototyping, producers can simplify the metal marking procedure and accomplish high-grade, economical manufacturing outcomes.
Tooling and Tools Essentials
Taking into consideration the crucial role that tooling design plays in the success of metal stamping jobs, understanding the crucial tools and devices needed is vital for accomplishing efficient manufacturing outcomes. Components hold the metal in location during the stamping procedure, making certain precision and repeatability. Investing in high-grade tooling and devices not only boosts manufacturing performance yet also leads to higher accuracy, lowered waste, and total expense savings in steel marking operations.
Manufacturing Refine and High Quality Control
Efficiently handling the manufacturing procedure and applying durable high quality control actions are necessary for making certain the success of steel marking projects. The production process in metal stamping entails a series of steps that should be carefully worked with to he said achieve optimum outcomes. It begins with the preparation of resources, adhered to by the setup of the stamping equipment and tooling. Operators then feed the materials into the press, where the stamping procedure occurs. Throughout this process, it is essential to keep an eye on the manufacturing line for any type of problems that may affect the quality of the stamped components.
Quality control in steel marking is vital to supply products that fulfill the called for specs. Inspecting the stamped parts at different phases of production helps determine any type of flaws early, avoiding pricey rework or scrap. Strategies such as dimensional examination, aesthetic assessment, and product testing are commonly employed to make sure the high quality of the stamped parts. By maintaining strict top quality control criteria, makers can support their online reputation for providing high-quality steel marked products.
Applications and Sector Insights
In the realm of steel stamping, the successful application of production processes and high quality control actions straight influences the performance and integrity of different market applications and provides valuable insights right into the sector's functional dynamics. Additionally, steel marking promotes the manufacturing of various house devices, including refrigerators, washing makers, and stoves, by supplying cost-effective solutions for producing long lasting and complex parts. Comprehending the applications and sector insights of metal stamping is essential for enhancing manufacturing processes and improving product top quality across different markets.
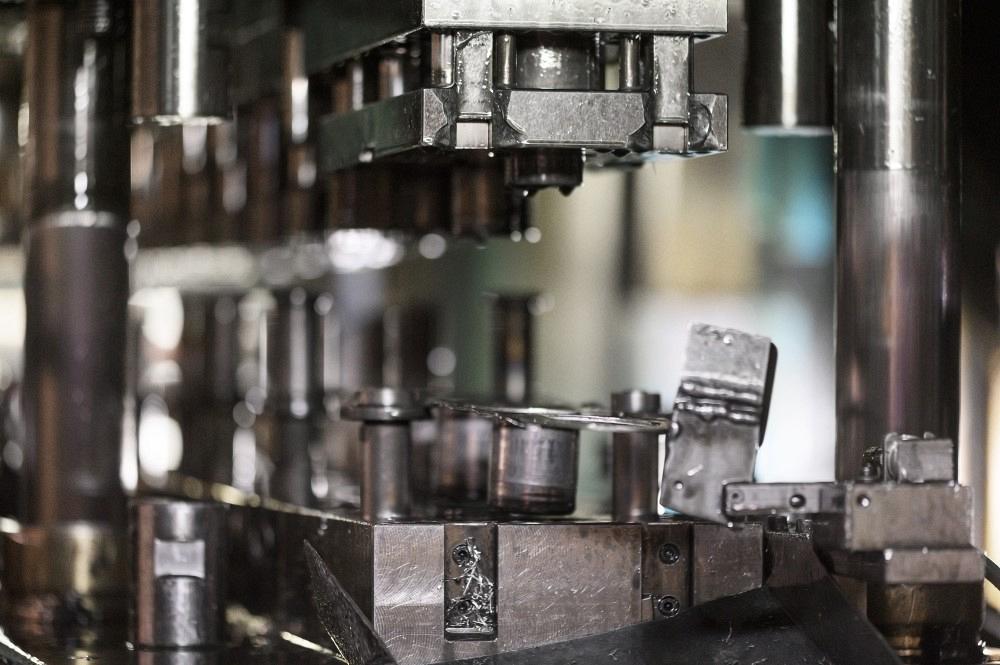
Conclusion
Style factors to consider, prototyping, tooling, tools, production procedures, and top quality control are crucial elements of steel marking. With its prevalent applications and sector understandings, metal stamping continues to be a versatile and effective production process.
Report this page